Digital is the new normal – what can the customers and partners of process and manufacturing industries expect now?
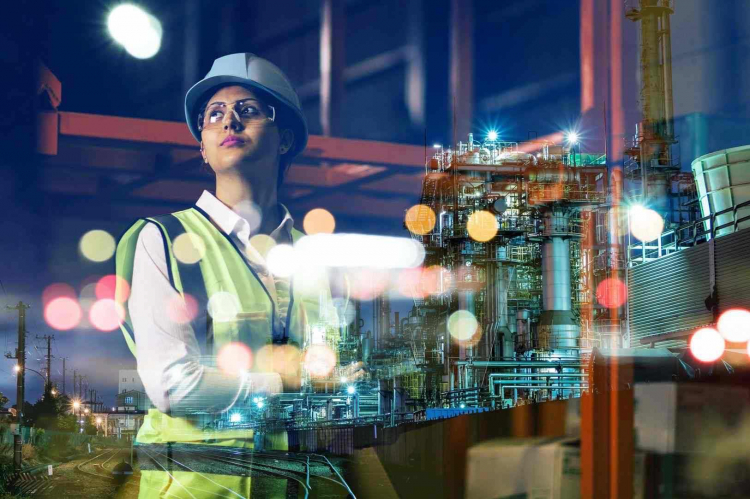
The development of digital is changing many industries and their value chain dramatically. Today, digital is a vital piece of everything. It sets new levels of ambition in many ways. This also happens in process and manufacturing industries. Customers that are using industrial assets strive for efficiency gained from advances in intelligent production equipment, intelligent operation of equipment and intelligent maintenance of equipment. This sets new requirements for industrial production and product capabilities. The following story shows how digital has changed the entire operational model in a sample value chain.
Margot is working as a wind farm site manager at a wind energy company in the Netherlands. After getting her coffee mug in front of her, she opens her laptop and SCADA application. She soon sees a cockpit view with gauges and multiple turbine icons on her screen. She decides to click one of the turbine icons. A giant wind turbine appears on the screen and starts to whirl and generate power steadily to the grid with its 2,5 MW capacity. However, this wind turbine does not exist in the physical world. It is a digital tein that only lives in the cloud and has a physical twin at the North Sea wind farm. As the site manager, Margot is always finding new ways to produce energy more efficiently, without increasing operation and maintenance (O&M) costs. A few minutes later, she is having a meeting with her account manager Bram, from the maintenance service provider.
After having a short chat about plans for the upcoming weekend, they start discussing the updates needed to the wind farms O&M plan. Margot wants to prepare the farm to increase its peak power by 7%, so it would be more productive for the next peak price of electricity. Bram has studied the analysis of different power setting operation scenarios and the associated wear and tear at different power outputs, by using the digital twin. His simulations and the results of the artificial intelligence (AI) based maintenance algorithm are looking good. However, there is one concern. A virtual sensor of one turbine gearbox is showing an alert. During the extremely high wind speed last night, there was a small increase in the gearbox oil temperature. This is an indication of a possible future bearing fault. A closer study would be required. A gearbox failure is always a major problem, especially when maintenance must be done ad-hoc, offshore and dependent on weather conditions.
A few hours later, at the gear manufacturing plant in Finland, the head designer Henri receives a phone call from his large Original Equipment Manufacturer (OEM) customer, a Dutch wind turbine manufacturer, who wants to set up an urgent meeting and get technical reassurance ready as soon as possible. In the past, this would have forced people to work overtime. However, Henri can now assign the task to one of his designers, Tiina. She starts to work on the digital twin data set of the operational history of the gearbox and the weather conditions. By comparing the data with the bearing manufacturer’s knowledge database and making additional simulations on the model, Tiina can propose an action plan for the next planned maintenance break.
What happened in this imaginary example is already possible in real life. Digital twins are being used for performance simulations under different conditions, to simulate service needs and product lifecycles. They support operative maintenance in failure diagnosis and fault prediction and adapt assets to real operating conditions. This technology has first been adapted where it has been most useful in minimizing operational downtime and expensive maintenance costs. A wind farm is a perfect example. Of course, a digital twin is just one example of digital development. There are many ways to have your digital product features.
Customers demand intelligence and efficiency
Customers are looking for new, intelligent ways to minimize their operational downtime and maintenance costs. This demand applies to intelligent production equipment, intelligent operation of equipment and intelligent maintenance of equipment. The digital capabilities demanded are, for example, higher productivity gained from optimized factory operations and faster workforce onboarding with increased work safety through augmented reality (AR) and virtual reality (VR).
When equipment becomes more intelligent there will be instant demand for a new type of services, for example, based on a subscription model, instead of an investment. In a subscription model, customers can acquire long-term assets without capital expenditures and get intelligent maintenance services included. This is possible today because algorithms can calculate maintenance needs according real equipment usage data and operational condition monitoring. There is also a recorded maintenance history of spare parts used already available, in many cases, to support decision making.
There is a customer demand for other new services and co-operation models. Demand for new intelligent services can also lead to new kind of customer contracts, based on service level agreements (SLA), instead of traditional time and materials. Customers now also expect more customization of products. They might want to get more closely involved in the innovation process and co-creation of product intelligence that would serve them best.
Industrial companies must respond
All industrial products must now have digital capabilities. It is important to start a dialogue with customers and partners to clarify their need in their product development, maintenance processes and operational management. You should clarify and refine your business model, as needed. Your old operational model might also be needed to change and become more agile, to be able to respond to customers and competitors.
Innovate beyond your current products and innovate new business models. The transformation must start within your company and the building of new digital skills and culture. An intelligent product contains new digital elements, based on data capturing capabilities and data analytics. Start designing standard interfaces to read equipment data for automation systems or operation management systems to increase autonomous and optimized operations. Reading equipment level data for maintenance purposes is a requirement. However, data must be also available in the real time and place independently to support alarms and early warnings of predictive algorithms. Some computation of data can be performed locally at a sensor or local network equipment level to detect anomalies and to fix them. This kind of edge-computing can be the fastest way to react, but centralized computing enables visibility over multiple assets and helps predictive algorithms to learn from all the data.
Intelligent services mean data-based services. They are based on intelligent products that support capturing data throughout their lifecycle. New digital services can optimize equipment maintenance and operational management of the equipment. Combined data from operational conditions with original manufacturing data of the equipment can bring new insights to product problem root cause solutions. Intelligent production is based on a digitally enabled factory, where the whole factory operations are being optimized. New state-of-the-art tools can be offered for blue- and white-collar employees to enable holistic decision-making and end-to-end transparent production.
Emerging technologies can be utilized in this development. Augmented reality, for example, can be used to make maintenance more efficient and to help maintenance personnel at the site to access information on the equipment. AR can also enable augmented self-service, where assisted customer employees themselves can undertake self-service on the equipment. AI might be applied to give further insights into the data as well freeing humans from searching anomalies. It could also offer classified findings from the equipment data or even ready-made proposals of corrective actions for humans to accept. Data and analytics in general are key enablers that can make equipment and processes intelligent and involve stakeholders at all levels.
Of the utmost importance today, however, is to think from an ecosystem point of view. It is necessary to understand how things work and who uses the data in different lifecycle phases. If you open your company’s boundaries to suppliers, customers and partners, it will be a major benefit for your company’s future success. Your company’s own and the suppliers’ R&D processes could also be enriched, by getting data back from the customer interface. Your OEM customers, using the company’s products in their equipment, could benefit from the collaborative sharing of product design data, as well as sharing know-how with knowledge databases.
Take the next step in your digital journey!
The time for digitalization hype is already over and the technology needed is here today. Industrial companies everywhere are embracing digital to meet their new customer expectations and respond to competitive threats. Digital is the new normal. It makes a difference in how you make it set you and your customers best. Due to the significant changes in industrial companies’ business environment and customer needs described above and in our previous blog, we have renewed our digital service offering. In our next blog, we will discuss our updated approach on how industrial companies can embrace digital and intelligence across their organization.